Not Your Grandmother's Yarn Shop
August 16, 2021
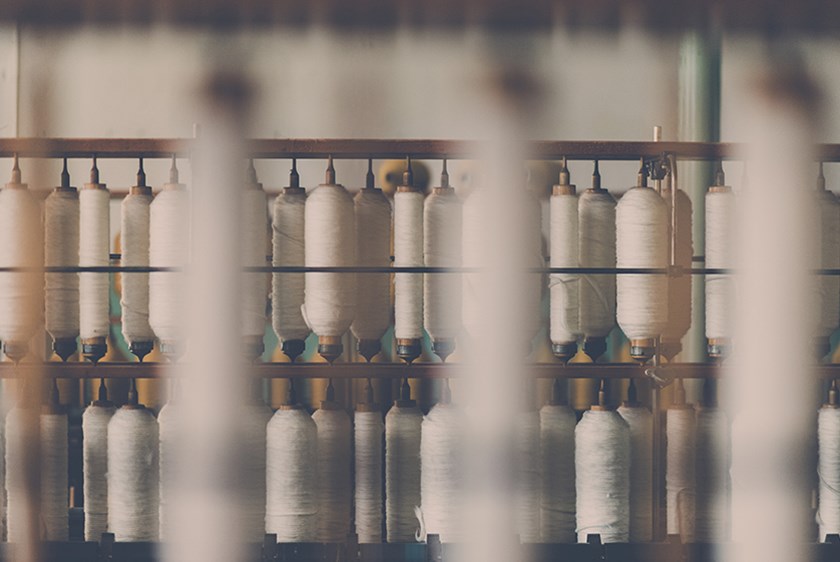
From the outside, it looks like an ordinary manufacturing plant and office building. But a few steps beyond the door, your original perceptions are shattered. This is AstenJohnson’s filament plant in Williston, Vermont, USA. Williston produces most of the filament “yarns” that AstenJohnson weaves into paper machine fabrics. And unlike the textile yarns of old, the filaments produced by Williston are high-tech and incredibly precise.
Keeping an innovative edge
Not many paper machine clothing suppliers have in-house filament production. But AstenJohnson considers Williston to be a major competitive advantage. Not only does it ensure the quality and quantity of yarns that AstenJohnson demands, it drives innovation. Being part of a larger value chain permits Williston to develop and produce specialized filaments that might not be profitable as a standalone product but are extremely valuable as part of AstenJohnson’s overall offering to customers.
Recognized pioneers
Diverse categories
A small percentage of Williston’s production is sold direct to other trades. This allows the Williston specialists to have a well-rounded perspective on industrial applications. For example, one of the big developments outside the paper industry has been the introduction of a non-halogen flame-retardant monofilament that is sold primarily to braiders for use in automotive applications and should be applicable to aerospace as well.
Williston has always been a home for exploration. PPS is a high-performance polymer that has become the industry standard in high-temperature applications, such as in the dryer section of a paper machine. It was first extruded into a monofilament fiber here. The same can be said for MONALLOY, an abrasion-resistant polymer blend used in forming fabrics. EcoLife™ — blended-polymer monofilaments for longer life and less energy consumption — was perfected at Williston, as was the first flat-warp yarn (the precursor to today’s “structured” yarns), which have captured a large share of the world's forming and drying markets.
Williston operates a “lab line” to investigate different polymers and adapt the properties of the monofilament to meet customer requirements. Fabric analysis, polymer analysis, melt tests, spectral analysis, and other tests are also performed on a daily basis. This is what keeps Williston in close touch with its internal customers in AstenJohnson’s weaving operations and with real-world customers in the mills.
Stretching is key
Making filaments for paper machine clothing is a specialized, niche manufacturing business. It is one part chemistry, one part fluid dynamics, one part thermal energy, a large part mechanical, and a small part magic.
Plenty of companies can extrude plastics through a static die to form a tube or rod. But the magicians at Williston are experts in stretching and relaxing the polymer as it is being extruded, building in the key properties required by AstenJohnson’s customers. It is no small task to stretch an extruded polymer into a yarn that is 0.11 mm in diameter — and to maintain that precise diameter over the entire length of up to 60 miles on a single spool. Add to this the fact that a production line is producing up to 120 spools at the same time, and you begin to appreciate the special knowledge and skills required.
Practical development
While there are some “pure” R&D projects, the vast majority of AstenJohnson’s monofilament development is in response to a specific capability that customers are looking for. A customer asks, “I need my fabric to do this; can you do it?” Sometimes the answer is found in the way the fabric is designed. Sometimes it comes from a different way of producing the yarn itself. More often, it’s a combination of the two. That is the key advantage of having Williston in the mix — working closely with the rest of the AstenJohnson team.