Old-School Terminology and Exceptional Durability for Packaging
April 19, 2021
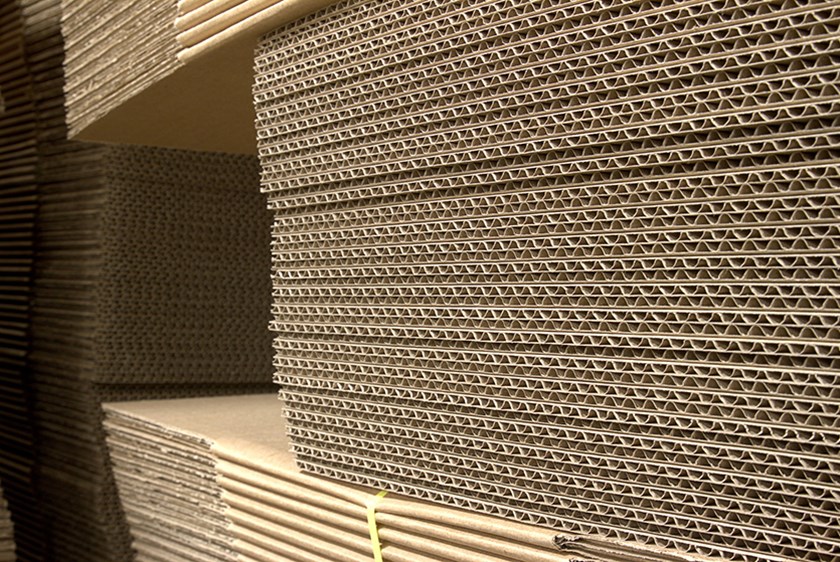
Warp, weft, knock, sheds, shuttles — all textile terms have been around for centuries, but our innovators still manipulate all this to provide products with optimized surfaces for printability and mechanical retention while maximizing wear volume for longer fabric life.
Longer floats enable the selection of higher-diameter weft yarns, which provide sacrificial wear volume to protect the load-bearing warp yarns. This is a critical feature for papermakers making heavier basis weight products, such as packaging grades.
It’s not as simple, however, as just using larger-diameter yarns. The innovation comes in combining the right materials with weaving techniques to masterfully float the weft yarns. AstenJohnson accomplished this with an innovation known as the Dura series of forming fabrics.
DuraLife™ fabrics utilize 12-shed weave patterns instead of the typical 10-sheds used by competitors. The benefit is longer than-standard machine-side “floats” and higher-wear volumes (up to 20% higher compared to conventional designs). The unique design provides flexibility for various yarn combinations to achieve the proper balance between paper-side and machine-side demands.
The special “locked-float” feature of DuraLife ensures very low movement of the weft yarns, improving overall stability. Lastly, one option in the Dura series, DuraLife MHD, has a unique warp-bound design that utilizes Center Plane Resistance™ technology to control initial drainage and to handle high drainage volumes on the paper machine.